Abbiamo visitato il nuovo stabilimento E-Mobility di ABB: ecco come si realizza un centro di eccellenza in Italia
di Massimiliano Zocchi pubblicata il 23 Giugno 2022, alle 15:58 nel canale Mercato Green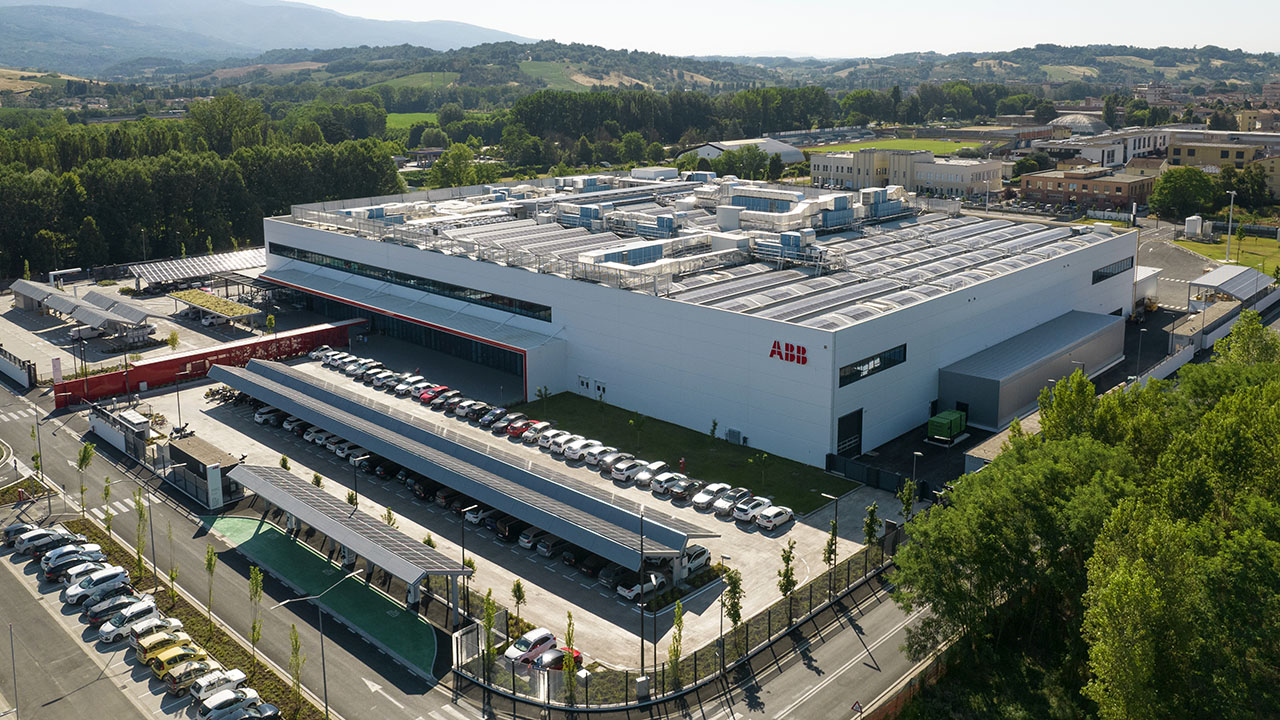
Anche in Italia si possono realizzare centri che siano d'esempio per tutto il mondo, ne è un esempio il nuovo stabilimento ABB a San Giovanni Valdarno, appena inaugurato, e dove vengono realizzate tutte le soluzioni di ricarica della multinazionale che ha sempre creduto nel nostro Paese
Quando si dice ABB, fa spesso rima con Italia, e da ora ancor più, con l'inaugurazione di un vero e proprio centro di eccellenza, l'E-Mobility center già operativo a San Giovanni Valdarno, nell'aretino. Abbiamo avuto nei giorni scorsi la fortuna di visitare lo stabilimento, assistendo anche al simbolico taglio del nastro, prima di addentrarci in tutti i reparti produttivi, per scoprire come nascono innovative colonnine di ricarica per veicoli elettrici.
Sì perché il nuovo sito produttivo si occuperà di tutti i prodotti ABB dedicati alla ricarica, a partire dalle più semplici wallbox, fino all'attuale prodotto di punta, Terra 360, colonnina DC ultrafast che già è in mano a diversi fornitori di ricarica europei e mondiali. Ma ABB non voleva solo costruire una nuova fabbrica, voleva dimostrare che anche in Italia si possono avere centri di eccellenza e stabilimenti moderni. In soli due anni ha quindi realizzato un sito che fa uso di energie rinnovabili, in larga parte prodotte in loco, ottimizzato per il risparmio energetico, e per il benessere dei lavoratori.
Appena arrivati si viene accolti da un grande parcheggio, e si nota subito che non è la classica soluzione. Quasi tutti i posti auto sono dotati di ricarica per veicoli elettrici o plug-in, con la divisione in più zone. Ci sono pensiline - tutte coperte di pannelli fotovoltaici - che hanno una wallbox in corrente alternata per ogni posto auto, mentre altri parcheggi, sempre coperti, sono dotati di colonnine fast e ultrafast, nel caso si debba ripartire poco dopo con il massimo della carica. Proprio in questa parte del parcheggio c'è una Terra 360 attiva e funzionante. Appena a fianco trovano spazio anche i sistemi di ricarica con palo e pantografo per bus e camion, utilizzati in questo caso per test e dimostrazioni.
Già dall'esterno tavolini e sedie posizionati tra aiuole tradiscono un ambiente di lavoro accogliente, apparenza confermata appena all'interno, circondati da pareti sempre verniciate di bianco e delicate luci LED, che abbiamo scoperto dopo essere tutte regolabili per evitare gli sprechi. Accendendo in un primo momento all'area mensa e svago abbiamo visto da subito i plus che possono avere i lavoratori. Il cibo è salutare e cucinato con cura, il bar è professionale e, oltre ai tavolini già citati, si può usufruire anche di tavoli da ping pong, calcio balilla, poltroncine, terrazze esterne arricchite da alberi e piante aromatiche. Tutto questo per far sì che il lavoratore renda al meglio quando si tratta di produrre le colonnine ABB.
È iniziato dunque il nostro tour nello stabilimento, partendo dal reparto di produzione delle schede elettroniche. ABB ha deciso di produrre decine di schede diverse direttamente da sé, utilizzando un mix di processi automatizzati e manuali. Un solo operatore può controllare il lavoro di diversi macchinari, dai laser ai saldatori automatici, ma la presenza umana è comunque fondamentale: tutte le schede vengono minuziosamente controllate, e rilavorate a mano nel caso si riscontrino delle imperfezioni.
Le schede passano dunque ai reparti di assemblaggio, in base al tipo di prodotti a cui appartengono. Nel caso delle colonnine DC, quelle più grandi e impegnative a livello di produzione, il lavoro viene svolto a stazioni. La colonnina, inizialmente poco più di un involucro vuoto, parte da una estremità del padiglione, e passo passo si muove tra diverse tappe dove vengono aggiunte tutte le parti, fino ad arrivare al prodotto completo all'estremità opposta della stanza. Qui viene anche effettuato un collaudo severo alle massime potenze, ma senza spreco di energia. Non vengono più utilizzate delle resistenze per simulare la batteria di un veicolo, ma l'energia viene reimmessa in rete, perdendo solo i punti percentuali dovuti al riscaldamento dei componenti ed alle perdite di conversioni e passaggi. Un processo certamente costoso, ma che contribuisce al concetto di sostenibilità dell'E-Mobility center.
Lo stabilimento trae tanta energia dall'impianto fotovoltaico che, sommando pensiline e tetto, raggiunge circa 600 kWp di potenza. Ma anche il resto dell'energia consumata è 100% certificata come rinnovabile. Oltre a questa presa di posizione fondamentale, ci sono altri accorgimenti nella stessa filosofia, come la raccolta dell'acqua piovana, o la riduzione dei rifiuti per ottenere il 100% di materiali riciclabili in uscita dalla fabbrica.
Eravamo rimasti alla nostra colonnina, che una volta collaudata passa al magazzino. Anche qui troviamo un mix di lavoro umano e automatizzato, con posti pallet caricati da un robot, ma anche il classico lavoro dei magazzinieri non manca. Anche il lavoro di imballaggio è fondamentale, visto che le colonnine dovranno affrontare in molti casi viaggi di centinaia se non migliaia di chilometri. Prima di uscire dal reparto di produzione, una cosa ci ha colpito: ci sono tantissimi giovani all'opera, e in prima analisi sembra rappresentino buona parte dei 500 lavoratori ad oggi impiegati a San Giovanni Valdarno.
Un'altra parte dei dipendenti, circa 70 persone, tipicamente ingegneri, si occupa del reparto ricerca e sviluppo, che qui a San Giovanni è interno alla fabbrica. Questo per far sì che chi sviluppa nuovi prodotti, o modifiche a quelli esistenti, sia a stretto contatto con i lavoratori che vanno poi effettivamente a realizzare il prodotto, con uno scambio di punti di vista, per individuare possibili migliorie. C'è anche un reparto, proprio per questo scopo, dove abbiamo visto gli addetti con più esperienza cimentarsi nell'assemblaggio di prototipi di nuovi prodotti. In questa fase non solo è fondamentale testare il corretto funzionamento di tutti i sistemi, ma anche verificare se la posizione dei componenti sia quella ottimale, o se ci siano modifiche da implementare per rendere, un domani, il lavoro in fabbrica più semplice.
L'ultima parte della ricerca riguarda i test i condizioni estreme, tramite camere climatiche in grado di simulare ambienti di lavoro particolarmente difficili, anche ben oltre quello che è lecito attendersi. Le camere possono passare anche da -100° a +100°, volendo anche in pochi minuti, grazie all'ausilio di azoto liquido e potenti riscaldatori, con potenze nell'ordine dei MW. Tale quantità di energia arriva direttamente dalla cabina di media di Enel. La stessa zona di test, oltre alle camere ovviamente sigillate, include anche uno spazio sufficientemente lungo per accogliere bus o camion, ed effettuare test di ricarica anche con questi veicoli.
Ultima, ma non per ordine di importanza, troviamo poi la camera anecoica. Questa particolare struttura, completamente sigillata dall'ambiente esterno, serve per azzerare l'inquinamento elettromagnetico normalmente presente nell'aria, così che l'antenna possa misurare solo le emissioni della colonnina nelle varie fasi di utilizzo. Si ha così una misurazione precisa, e la verifica che il punto di ricarica sia sicuro per i futuri clienti. Infine esternamente allo stabilimento, per questione di sicurezza, sono presenti altre camere chiuse, dove i nuovi prodotti vengono testati alla massima potenza (ancora una volta, senza sprecare l'energia utilizzata) in condizioni di stress superiore al reale e con cicli ripetuti e continui, 7 giorni su 7, giorno e notte, 365 giorni all'anno. In questo modo in un periodo che va dai 6 mesi a un anno e mezzo (a seconda del prodotto) ABB può simulare un utilizzo di circa 10 anni.
Per chiudere il nostro reportage sul centro E-Mobility ABB di San Giovanni Valdarno vi lasciamo anche qualche dato. L'investimento per la realizzazione è stato di 30 milioni di dollari, per un'area totale di 16.000 metri quadrati. Di questi, circa 3.200 metri quadrati sono dedicati all'R&D, per sviluppo e prototipazione. La fabbrica consentirà di produrre fino a 10.000 colonnine in corrente continua all'anno, in pratica una ogni 20 minuti grazie alle sue sette linee di produzione. La struttura di Valdarno mira, inoltre, a ottenere la certificazione gold level LEED, lo standard indipendente riconosciuto a livello mondiale per la progettazione, la costruzione e la gestione di edifici eco-compatibili.
9 Commenti
Gli autori dei commenti, e non la redazione, sono responsabili dei contenuti da loro inseriti - infoTutti quelli che conosco che ci lavorano sono entusiasti, sia per l'ambiente di lavoro, sia per il trattamento lavorativo/economico. Un bel plus per la mia cittadina!
Ennesima multinazionale "mastica ferro".
Anche in Italia si possono realizzare centri che siano d'esempio per tutto il mondo, ne è un esempio il nuovo stabilimento ABB a San Giovanni Valdarno, appena inaugurato, e dove vengono realizzate tutte le soluzioni di ricarica della multinazionale che ha sempre creduto nel nostro Paese
Bravi ragazzi
E' un po' come Nikon nel settore della fotografia, è l'unica azienda di questo settore che cura molto la diffusione della cultura fotografica contrariamente a Canon, Fujifilm, Leica e compagnia bella ...
E' inutile avere le colonnine quando la rete non regge il carico neanche dei condizionatori
https://www.repubblica.it/cronaca/2...lano-354530577/
https://www.repubblica.it/cronaca/2...lano-354530577/
Se il petrolio che metti nel tuo serbatoio lo usi invece per produrre elettricità in una centrale termoelettrica, ottieni quasi il doppio dell'elettricità che ti serve per le colonne di ricarica (quindi potrai anche accendere il condizionatore), infatti una centrale termoelettrica moderna ha un'efficienza di più del 60% mentre il tuo motore a scoppio ha un'efficienza del 35%. Basta balle dai no-elettrico.
Ma quali balle?
I black out sono reali, se tu avessi provato ad approfondire la mia affermazione invece di comportarti da fanatico, avresti capito che il problema non è la generazione di energia, ma l'inadeguatezza dell'infrastruttura di trasporto.
P.S: non sono no-elettrico, semplicemente ritengo che la mobilità elettrica non sia sufficientemente matura al livello tecnologico (e acquisterei volentieri un'auto elettrica se ne trovassi una adatta alle mie esigenze)
Devi effettuare il login per poter commentare
Se non sei ancora registrato, puoi farlo attraverso questo form.
Se sei già registrato e loggato nel sito, puoi inserire il tuo commento.
Si tenga presente quanto letto nel regolamento, nel rispetto del "quieto vivere".